
Tool/Die Construction
The process begins with the construction of a high-precision tool or die, crafted from durable materials to shape the wax patterns used in the casting process.
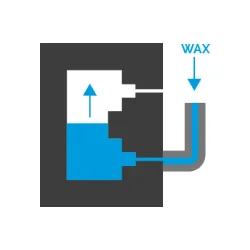
Wax Injection
Molten wax is injected into the die to create a detailed wax pattern that replicates the final casting.

Wax Assembly
The individual wax patterns are then assembled onto a central wax runner system, forming a tree-like structure to facilitate multiple castings in a single mold.

Slurry Coating
The assembled wax tree is repeatedly dipped into a ceramic slurry, creating the initial layer of the ceramic shell mold.

Stuccoing
After each slurry coating, the wax assembly is sprinkled with fine sand, or stucco, to build up the ceramic shell’s strength and thickness.
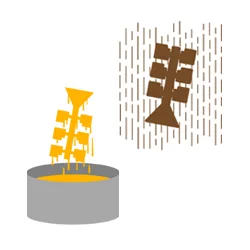
Repeat Slurry Coating and Stuccoing
Steps 4 and 5 are repeated multiple times to ensure a robust and durable ceramic shell capable of withstanding the casting process.

Dewaxing
The ceramic-coated wax assembly is heated to remove the wax, leaving behind a hollow ceramic shell.

Casting/Metal Pouring
Molten metal is poured into the preheated ceramic shell, filling the cavity left by the wax patterns.

Shell Removal
Once the metal has solidified, the ceramic shell is broken away, revealing the raw metal casting.

Runner, Riser, and Gate Cut-Off
The individual castings are separated from the central runner system, and excess metal is removed.

Finishing/Fettling
The castings undergo various finishing processes to remove any surface imperfections and achieve the desired surface quality.
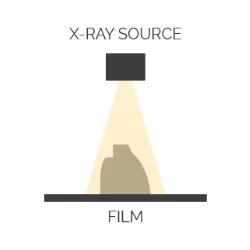
Casting Inspection
Each casting is meticulously inspected for dimensional accuracy and quality to ensure it meets our stringent standards.

Machining
Depending on the application, castings may undergo additional machining to achieve precise dimensions and tolerances.
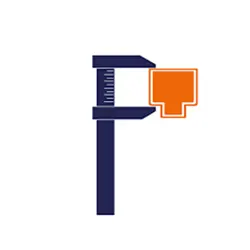
Final Inspection
A thorough final inspection is conducted to ensure every casting meets the required specifications and quality standards.

Packing and Dispatch
The finished castings are carefully packed to prevent any damage during transit and dispatched to our clients, ready for use in their applications.